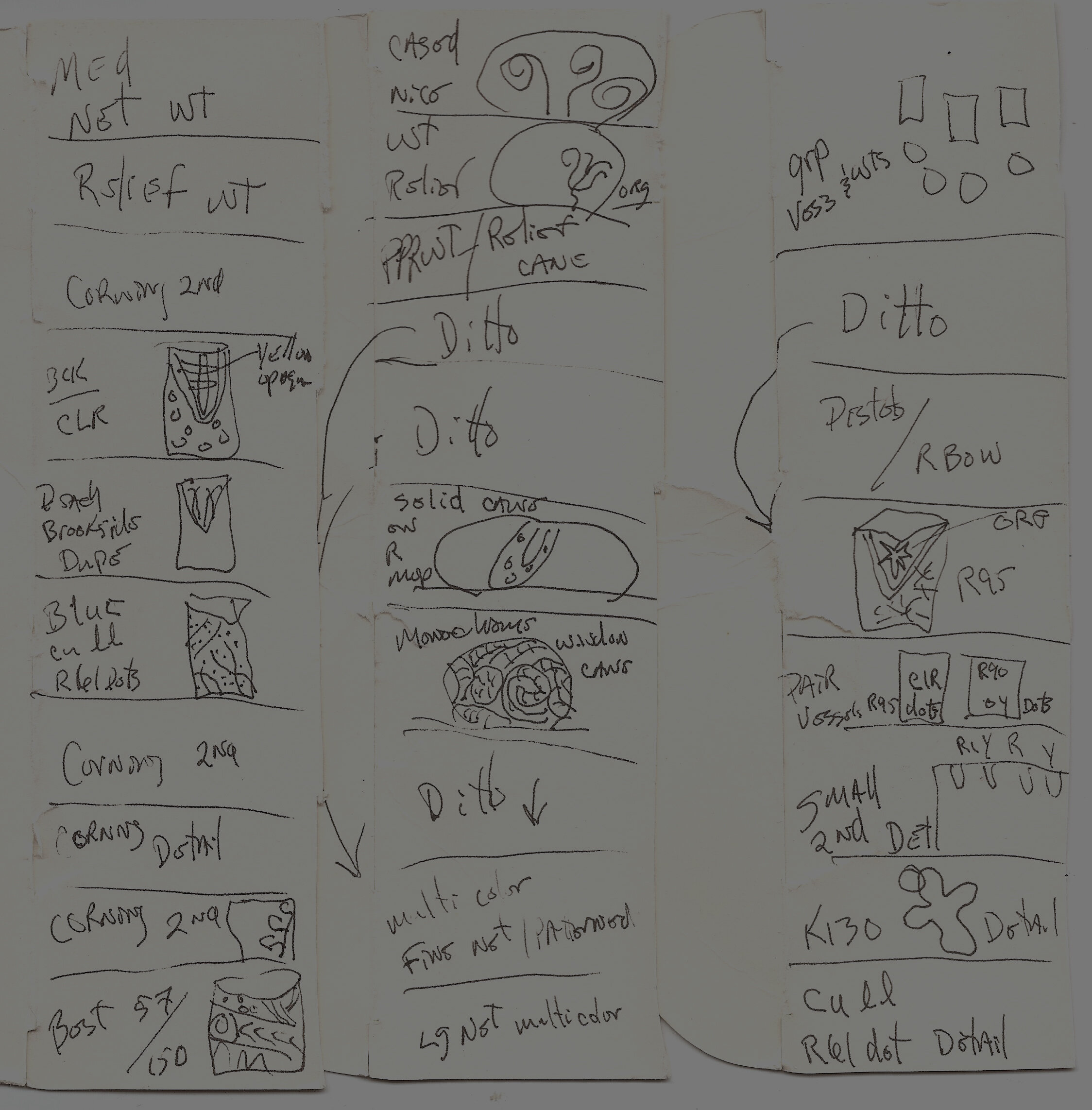
Information about Kenny’s work and process in his own words and by his own hand.
Kenny Walton wrote in the 90’s about making his glass:
Technical Process for Offhand Blown Glass
All the glass was made and designed by me alone, without assistants, in my studio on our acreage in rural eastern Nebraska.
I make paperweights and square glass vessels, each made one at a time. The process is made in several steps. First, I make the colored glass cane used for decoration by melting colored glasses and then drawing them out into long thin rods. The cane can be either transparent or opaque. By adding cane together, it can be made more complex – having straight lines of contrasting colors, lines that spiral around the cane, or layers within and outside of the cane. The cane is made in great variety, and I keep a huge “palette” of canes ready on hand.
I melt clear glass in my furnace in crucibles at about 2200-degree Fahrenheit. Glass is gathered out on the end of the blowpipe, and accumulated in layers by dipping into the molten glass. By reheating the “gather” every few minutes in a second furnace called a “gloryhole” the working time can be extended as long as necessary to complete the decoration and the forming. The glass needs to be kept at an ideal temperature for blowing the bubble into the interior and for shaping. Tools and wooden “blocks” of different shapes help to shape the form. Color chunks of stock glass can be melted into the layers of gather, so an appearance of a colored glass base allows for great variety, without needed to have crucibles of different colors.
Between reheats I prop the glass up and apply the cane to the exterior of the gather by melting it onto the surface slowly with a torch. This slow repetitive process accumulates into the design you see. Potentially each successive layer can be decorated. I compose the pieces as I work, and that can take hours sometimes.
When the design is ready to my satisfaction, is can be further worked and blown out for vessels or kept solid and dense for paperweights. Then the piece is transferred to the punty rod which is attached on the end opposite the blow pipe, and is broken off the pipe by scoring and a sharp tap. The piece is then worked to open up and shape the form while on the punty, all the while with reheating in the gloryhole. Upon completion each piece is knocked off the punty, and carefully put into an annealing oven. This allows for slow cooling at an appropriate rate, which relieves the stress in the glass.
This final stage is stressful and exciting, and can happen more quickly than the decoration stage. Yet all the time and skill invested in working each piece for several hours is rewarding and risky, and carries all my research and experience for something unique.